First Commercial Quantities of EPA-Approved Cellulosic Ethanol Sold--With a Little Help from Michigan Tech
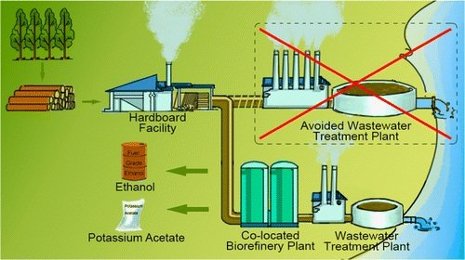
Scientists and engineers—including several at Michigan Technological University—have been talking for years about biofuel, particularly cellulosic ethanol, which is fuel made from trees and other woody plants. The stumbling blocks have been huge and progress, slow. But the Environmental Protection Agency’s (EPA) Renewable Fuels Standard mandates that cellulosic ethanol be blended into gasoline for use in vehicles, so the need is immediate.
Now, the first commercial quantities of cellulosic ethanol generated from woody biomass that meets EPA standards have gone to market. American Process Inc. (API), an Atlanta-based company that develops renewable materials, fuels and chemicals from biomass, is producing the cellulosic ethanol at a demonstration plant in Alpena, Mich.
The news gets even better. The biorefinery that is producing commercial quantities of cellulosic ethanol is doing it by converting a wastewater stream from the nearby Decorative Panels International plant into biofuel, saving massive amounts of energy that used to have to be used to treat the wastewater. The plant is also producing a woody biomass-based potassium acetate runway de-icer in a process that generates up to 45 percent less greenhouse gases than the production of conventional potassium acetate.
With funding from the US Department of Energy and the State of Michigan, Michigan Tech scientists and engineers helped make all of these landmark achievements possible.
Cellulosic Ethanol
API’s chief technology officer, Vesa Pylkkanen, is a graduate of Michigan Tech. When API decided to try to figure out how to use the waste from the hardboard panel plant to make cellulosic ethanol in commercial amounts, Pylkkanen knew just whom to contact.
API asked David Shonnard, professor of chemical engineering at Michigan Tech, and Susan Bagley, professor emerita of biological sciences, to study the waste stream from the Decorative Panels plant. Shonnard, who holds the Robbins Chair in Sustainable Use of Materials and heads Tech’s Sustainable Futures Institute, and his PhD student, Jifei Liu, analyzed the wastewater to determine the make-up of the woody biomass in it. Once they knew what they were working with, they used hydrolysis—a chemical reaction involving water and dilute acid—to identify the best way to convert that kind of biomass to fermentable sugars, a key step in the process of producing cellulosic ethanol.
Bagley and her PhD student, Stephanie Groves, then conducted experiments to improve the adaptation of yeast microorganisms to most efficiently ferment the unique mix of 5-carbon sugars produced from the plant’s wastewater.
The Michigan Tech researchers submitted their findings to API to help the company fine-tune its engineering designs.
“Dr. Shonnard and his colleagues’ work led to a better understanding of the microbiological pathways that support fermentation of the 5-carbon sugars and the impact of biomass-derived inhibitors on fermentation performance,” said Kim Nelson, API vice president. In short, she said, Shonnard and Bagley’s work formed a solid scientific foundation for the success of API’s Alpena Refinery demonstration project.
Greenhouse Gases
Shonnard’s research group also conducted environmental life cycle assessments of the Alpena Biorefinery, to understand the carbon footprint of its cellulosic ethanol production process and its effects on greenhouse gas emissions. They found that the entire life cycle greenhouse gas emissions from the plant’s cellulosic ethanol were only 25 percent that of petroleum-based gasoline, and when the study was based on EPA methodology, even lower.
“This work was paramount for obtaining certification from the EPA under the Renewable Fuels Standard, which requires the fuel to reduce greenhouse gas emissions by at least 50 percent,” said API’s Nelson. It also helped API market the de-icer to airports and to the federal government. “Both are keenly interested in reducing the levels of greenhouse gas emissions from airplanes and the associated support processes and infrastructure,” she explained.
Shonnard says the results of Michigan Tech’s collaboration with API underscore the need for university-corporate-governmental partnerships. “This project demonstrates that when university researchers team up with motivated private sector companies and state and federal funding sponsors, good things can happen.”
Michigan Technological University is an R1 public research university founded in 1885 in Houghton, and is home to nearly 7,500 students from more than 60 countries around the world. Consistently ranked among the best universities in the country for return on investment, Michigan's flagship technological university offers more than 120 undergraduate and graduate degree programs in science and technology, engineering, computing, forestry, business, health professions, humanities, mathematics, social sciences, and the arts. The rural campus is situated just miles from Lake Superior in Michigan's Upper Peninsula, offering year-round opportunities for outdoor adventure.
Comments