A Call to Change Recycling Standards as 3-D Printing Expands
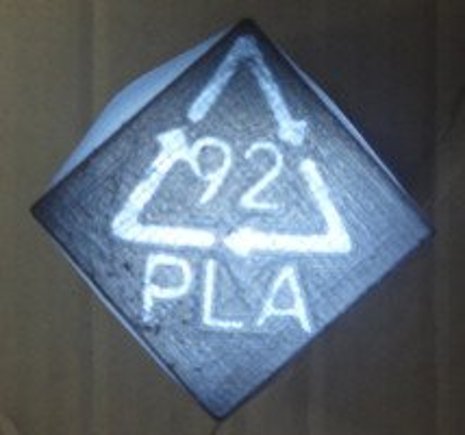
The 3-D printing revolution has changed the way we think about plastics. Everything from children’s toys to office supplies to high-value laboratory equipment can be printed. The potential savings of producing goods at the household- and lab-scale is remarkable, especially when producers use old prints and recycle them.
Buying plastic filament for printing can be expensive, says Joshua Pearce, the lead researcher in the Open Sustainability Technology group at Michigan Technological University. Pearce and his students have whittled the cost of printing to ten cents per kilogram — down from $30 per kilogram.
They made this leap by recycling plastic that had already been printed, using a recyclebot and plastic resin codes developed by the team.
In a new paper from the research group, published in Resources, Conservation and Recycling, the authors lay out how they achieved this price reduction and how to recycle 3-D printed objects more broadly.
“The centralized paradigm of both manufacturing and recycling is being challenged by the rise of 3D printing,” Pearce says, explaining that labeling and reusing materials is voluntary.
Current labeling schemes, however, are not detailed enough for 3-D printed recycling. Plastic is not just plastic; there are many kinds, and specific polymers behave in specific ways — which makes a big difference for 3-D printing.
“We want to know about polymers the same way a chemist would,” Pearce says, admitting that the seven codes in the US recycling system fall short. In comparison, China has 140 codes for different polymers. “Currently, the most common 3-D printed plastics are grouped in the category seven polymers in the US,” he adds.
That seven category is the catch-all group and means little as a label. Most widely used and conventionally produced plastics fall into the first and second categories — the same groups that cover plastic water bottles and milk jugs. These can be recycled for 3-D printing, but the two most common plastics for 3-D printing are PLA (polylactic acid) and ABS (acrylonitrile butadiene styrene). PLA is often used as biodegradable dinnerware and ABS is the hard plastic of Lego blocks. Although they’re distinctly different, being lumped with so many others in the seven categories makes it difficult to reuse these plastics in 3-D printing.
To overcome these issues, Pearce and his team developed a new resin code identification system based on the Chinese codes. They focused on polymers that could be recycled in 3-D printing and made the system expandable to accommodate innovations in printing and plastics.
“We also demonstrated how to incorporate recycling symbols into 3-D printed objects using open-source and parametric scripts for our new print codes,” Pearce says. The scripts are freely available on Appropedia.
The labels themselves are novel in 3-D printing. Standard recycling labels are small, slightly raised and often placed on the bottom or another convenient location. But with 3-D printing, the labels can be woven into the design itself. A pencil holder can reveal its secret polymer type as light shines through its plastic bottom or a broken screwdriver handle can be cracked open to show its code number. Neither is possible with conventional manufacturing.
The inventive ways to use recycling labels along with the new code system and free scripts are a big step towards better 3-D printing recycling, which is good for the environment. Pearce hopes to make the practice widespread.
“To make this actually happen, the coders for the slicing software need to make this an option,” he says. “So we’re sharing the source codes so they can incorporate them into their software for free, so everyone can use it.”
The paper was co-authored by Pearce and students Emily Hunt, Chenlong Zhang, and Nick Anzalone. Available: Open access pre-print.
Michigan Technological University is an R1 public research university founded in 1885 in Houghton, and is home to nearly 7,500 students from more than 60 countries around the world. Consistently ranked among the best universities in the country for return on investment, Michigan's flagship technological university offers more than 185 undergraduate and graduate degree programs in science and technology, engineering, computing, forestry, business, health professions, humanities, mathematics, social sciences, and the arts. The rural campus is situated just miles from Lake Superior in Michigan's Upper Peninsula, offering year-round opportunities for outdoor adventure.
Comments