Michigan Tech researchers are bringing mining into the modern age using novel technologies to advance the industry toward goals of reliable supply chains and net-zero emissions.
Chemical engineer Lei Pan remembers the fascination and promise he felt as an undergraduate when his professors demonstrated how flotation works in mineral processing.
"I was very interested when the bubbles were floated and loaded with shiny brassy-colored copper mineral particles. I was hooked!" says Pan, smiling widely at the memory. "I was also very interested in helping the graduate students who I worked with at that time in processing iron ores using magnetic separators and making green pellets out of processed iron ores."
These days, Pan holds the teaching role—and the associate professor wants his students to feel the same thrill and deep appreciation for mineral processing he did. That's why Pan teaches Huskies in the field, taking them to mining operations on the sprawling spine of Upper Midwest iron ranges, including the nation's only nickel mine. Each year, there's one field trip involving numerous students and mining-associated Michigan Tech faculty and staff members.
"I don't bring the paper knowledge to students; I love to bring students to the mines," says Pan. "You can feel the rocks, feel the heat from the furnace, see the massive operation. I always want students to understand that the mining industry is a vibrant, resident industry."
But Pan's vision for elevating and sustaining the mining industry goes further than field trips and lab work. He is helping create a future where the United States is no longer dangerously dependent on unreliable international supply chains for critical minerals. He sees a future where, at the same time that the raw materials needed to power society and industry are responsibly extracted, carbon emissions are isolated and safely sunk into the remaining rock.
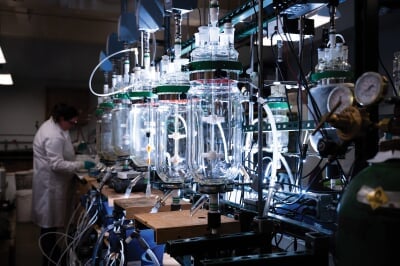
His method, a novel variation on the flotation process that so captivated him during his undergraduate studies, dramatically speeds up carbon dioxide sequestration while separating out urgently needed minerals from mine waste. The process, which required developing and building a flotation column that can capture larger quantities of higher-quality minerals, has made its way from his Michigan Tech lab to regional mining operations, including Eagle Mine in northwestern Marquette County.
A subsidiary of Toronto-based Lundin Mining, Eagle Mine is currently the nation's only nickel mine. Pan is also working with the NewRange copper nickel mine in Minnesota, a joint venture between PolyMet and Teck American Inc.
Froth flotation is a settled technology with numerous applications in industries ranging from paper to oil sands. In mining, it's commonly used to separate gangue—the industry term for unwanted minerals or impurities—from the desired minerals.
"This process uses free and most abundant carriers—air bubbles—to separate various mineral compositions, depending on the certain types of minerals that the bubbles can pick up. A specialized chemical is added to render the certain mineral particles hydrophobic—or tending to repel water," Pan explains.
The notion that net-zero emissions are an attainable goal in an industry long known for its environmental hazards is not unsubstantiated green-washing. The federal government has supplied considerable research funding for partnership efforts that pair mining industries with technological innovators. Michigan Tech and Eagle Mine are co-recipients of $10.6 million in funding aimed at proving new research technologies that develop sustainable processes to supply critical minerals that ensure a domestic battery supply chain.
Of that funding, $2.5 million from the US Department of Energy (DOE) through its Advanced Research Project Agency-Energy (ARPA-E) grant program is dedicated to helping mines in Michigan's Upper Peninsula and Minnesota achieve net-zero emissions while extracting critical minerals from mine tailings. An additional $8.1 million in federal funding through the 2021 Infrastructure Investment and Jobs Act will be used to open a pilot facility to scale up mine waste reprocessing and battery recycling technology starting in summer 2025.
Out of Sight, Out of Mine
Critical minerals are those that, aside from minerals used for fuel, are deemed necessary for national and economic security. If you use a cell phone or laptop computer, have a medical implant, travel by plane, drive a car, use home appliances, or make use of electrical transmission lines—you rely on critical minerals, too.
"People don't appreciate that what we use every day is either coming from mining or recycling," says Pan. "Mining has always been part of the energy structure, from coal to natural gas and oil. Mining will continue to be a part of supplying the raw materials."
The continued relevance of mining and the need for research and development (R&D) has drawn Pan deeper into the field.
"It has been a pleasure to work with the mining industry. Being able to directly communicate with industrial professionals and understand the challenges faced in the industry can greatly help the R&D efforts," he says. "In addition, students are better educated and motivated by the real problems faced in the industry and will be better positioned for their careers."
Those students and R&D efforts will add to what Pan calls the "massive impact" of mineral processing and extractive metallurgy operations on society. "Globally, billions of tonnes of ores have been processed using various mineral processing unit operations such as froth flotation," says Pan. "The US, for instance, produces 29 million metric tons of pig iron and 88 million tons of steel, and 1.17 million metric tons of copper annually. In all cases, the majority of ores are first processed by typical unit operations, including crushing, grinding, froth flotation, and magnetic separation."
"It's very important to lower both the energy consumption and greenhouse gas emission in all phases of mining operations, including mineral processing and metallurgical processing," he adds. "R&D is essential to lower the environmental impact of the mining operation while recovering critical minerals from unconventional resources including mine tailings and mine wastes."
Pan's project funded by ARPA-E aims to do that. "The goal is to recover critical minerals from mine tailings while achieving a negative emission of the entire operation."
Pan's team has also created urgently needed paths forward for expanding lithium-ion battery recycling. They were the first to introduce froth flotation technology as a method of recycling the batteries.
"The froth flotation technology enables a separation of anode and mixed cathode materials from spent lithium-ion batteries. Both recycled electrode active materials can be then recycled into new materials," says Pan.
"Metal recycling has been and will continue to be an important player in the future," he adds. "Unlike fossil fuels, critical minerals are infinitely recyclable during their life cycle."
Launching a Critical Hub
Research universities continue to play an essential role in determining mining's future. At Michigan Tech, Pan is leading a charge to initiate more mining-related research by establishing the Center for Critical Minerals. He views the new center as a way to revitalize and reimagine the work the University has been conducting since its inception.
"This old industry has a future. Every society needs raw materials. It's all coming from the mines."
"Michigan Tech began as the Michigan School of Mines in 1885 with a strong reputation in the mining industry for its talents," he says. "However, since the closure of the US Bureau of Mines in 1996, research activities in mining and mineral processing have been low. The Center for Critical Minerals aims to address the needs of both science and education related to critical minerals and the materials supply chain."
The center will assist members in acquiring external funding for research, grow internal and external partnerships and capacity to achieve broader impacts, and serve as a hub in providing critical technical service to the industry. It will also create an inclusive community for all research scholars and provide educational opportunities at the graduate, undergraduate, and high school levels.
It's a new future for an age-old industry. It's R&D for what tomorrow needs.
Michigan Technological University is an R1 public research university founded in 1885 in Houghton, and is home to nearly 7,500 students from more than 60 countries around the world. Consistently ranked among the best universities in the country for return on investment, Michigan's flagship technological university offers more than 120 undergraduate and graduate degree programs in science and technology, engineering, computing, forestry, business, health professions, humanities, mathematics, social sciences, and the arts. The rural campus is situated just miles from Lake Superior in Michigan's Upper Peninsula, offering year-round opportunities for outdoor adventure.