Plastic-sourced protein powder developed by Michigan Tech researchers could help solve two prominent global issues: hunger and plastic pollution.
Of all the world's problems, Stephen Techtmann, assistant professor of biological sciences at Michigan Tech, has two on his mind. One is that the world's population is growing and hunger is growing with it. According to the United Nations, 690 million people—8.9 percent of the world's population—are hungry. Partially because of rampant poverty and climate change, the total is expected to increase by 10 million people in one year and 60 million in five years. If nothing changes, the world will fall far short of the United Nations' goal to reach zero hunger by 2030.
The other problem on Techtmann's mind is plastic—a lot of plastic. Of the 6.3 billion tons of plastic made every year, 79 percent accumulates in landfills, according to the United Nations' Environmental Programme. By 2050, Earth's oceans will have more plastic than fish when compared by weight. And plastics aren't going away anytime soon, either. Some can degrade in 10 years. Others take hundreds.
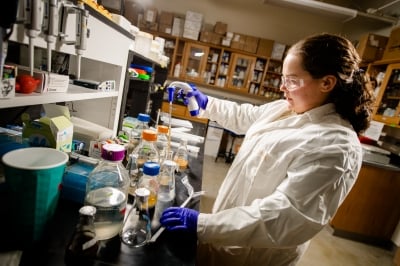
The process converts plastic into compounds using heat and a reactor that deconstructs the material’s polymer chains. The oil-like compound is fed to a community of oil-eating bacteria Techtmann’s lab has been studying. Bacteria grow rapidly on the oily diet, producing more bacterial cells composed of roughly 55 percent protein.
Could one problem solve the other? Techtmann thinks so. He and a multidisciplinary team of engineers, chemists, and biologists are breaking those landfill- and ocean-clogging plastics down to be recycled into useful products, like lubricants, or in what he sees as a more impactful discovery, edible protein powder.
The entire process currently works on a lab bench. Techtmann's initial goal is to deploy the system cheaply and easily in disaster areas or environments experiencing food shortage, where it can address the immediate goal of hunger while relief efforts mount.
It's as simple as "put plastic in one end and get this powder out of the other," he says. "If we can put those units into a single box that can be deployed on a truck or built in a field, then we can help get people food quickly when they need it the most, and it becomes one of the tools we could use in how we process plastic."
He sees potential beyond disaster relief too. If the stars align (and with a good marketing campaign) plastic-turned-protein-powder could become the next Impossible Meat. "If this becomes more widely available, it could go from food to survive to food to thrive," he says.
Raising Eyebrows
Many find the idea of eating something that began as plastic to be weird. Techtmann is used to it. "I don't want to eat plastic either," he says. He knows his discovery has a public relations problem. However, he's not trying to push a protein powder with plastic chunks. Instead, he deploys bacteria to transform the plastics into something entirely new.
Techtmann feeds the plastics to oil-eating bacteria that chew them up and use them as fuel to grow. After the plastics are eaten, the end result doesn't look like plastic at all—it resembles a yeast byproduct that comes from brewing beer. This majority-protein byproduct is then dried out and turned into an edible powder.
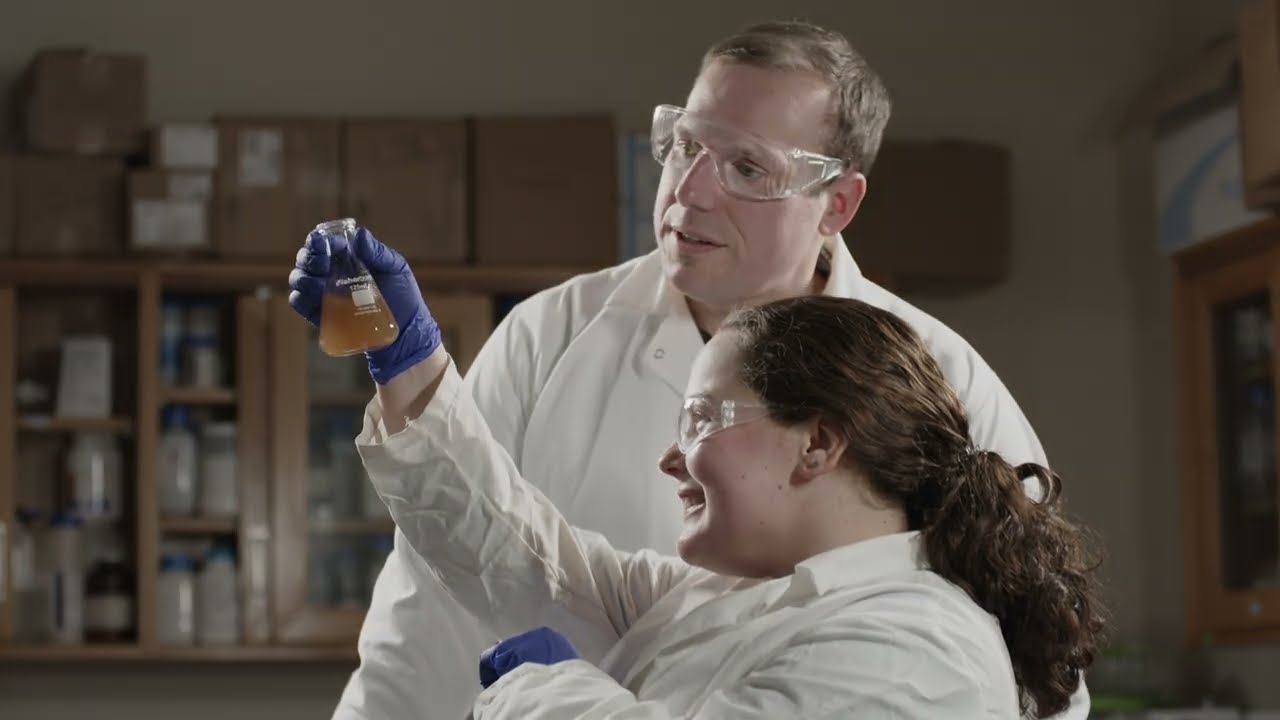
Discover Oil-eating Bacteria that Serves the Greater Good
In the award-winning Techtmann microbiology lab, students work alongside the faculty researcher to identify microbial communities that could clean up oil spills, munch up plastic waste, and break down non-edible plant biomass to solve two world challenges: hunger and pollution.
The official name of the project is BioPROTEIN (Biological Plastic Reuse by Olefin and Ester Transforming Engineered Isolates and Natural Consortia). Techtmann's team includes MTU's Rebecca Ong, assistant professor of chemical engineering, David Shonnard, professor of chemical engineering, and Joshua Pearce, an electrical and computer engineer, as well as Ting Lu, professor in bioengineering from the University of Illinois at Urbana-Champaign. The group is funded by an award from the Defense Advanced Research Projects Agency (DARPA) for up to $7.2 million. Part of the US Department of Defense (DoD), DARPA funds breakthrough technologies and capabilities for national security.
The DoD is interested for some of the same reasons Techtmann is. "Plastic is a difficult waste to deal with," says Techtmann, adding that the DoD often deploys soldiers in areas where access to food is a problem. Techtmann's plastic-to-protein box could be a solution, allowing military personnel to proceed with operations despite limits on how much food they can bring.
"We're trying to take plastic or mixed waste from military operations to make it into something useful in the field," he says. "Then they don't have to dispose of the waste, and can fuel themselves and the people they're helping too."
Techtmann and Lu have also received the €1 million Future Insight Prize from Merck KGaA, Darmstadt, Germany, a leading science technology company, to fund another branch of the project: using synthetic biology approaches to augment probiotics, improving food quality by increasing nutrient contents, boosting resistance to foodborne pathogens and adding personalized therapeutic benefits. "The foundation of this research greatly benefited from DARPA's investment. The grant from Merck KGaA, Darmstadt, Germany lets us build off that," Techtmann says.
A Difficult Waste
Breaking down plastic isn't easy. Ironically, its structure—long, difficult-to-break polymer chains, the same property that makes plastic such a widely used material—also leaves it lingering in oceans and landfills for up to hundreds of years.
While it's possible to recycle some plastics, most of them just aren't. According to a study from the University of Georgia, as of 2015, only 9 percent of the virgin plastics produced on Earth to date had been recycled, and 79 percent ended up in landfills or the natural environment. That's not just for one reason, but many—including how plastics are valued and because current recycling infrastructures can't process all plastics.
For example, a plastic bottle can easily be recycled into another plastic bottle because the quality of the plastic is high—and most people know to toss an empty water bottle into a recycling bin. But plastics used in shopping bags and protein bar wrappers are lower quality, and current recycling infrastructure isn't equipped to turn them into something else.
Plus, there isn't always a market for this lower-grade recycled plastic. In 2019, China stopped importing other countries' waste for recycling and reuse. The value of plastics nosedived. Even though numbers have recently rebounded, it doesn't mean the market won't scuttle the price of plastic again, leaving even the most easily reused items in the trash.
"Even though we're able to throw a lot of those plastics into a recycling bin, they're not all valuable enough to be sold to someone else to recycle them," Techtmann says.
A Meeting of Mindsets
Techtmann likes to use science to solve real-world problems, and even early in his career, he investigated bacteria as potential solutions. Spurred by the 2010 Deepwater Horizon disaster that hemorrhaged 210 million gallons of oil into the Gulf of Mexico, he studied whether oil-eating bacteria could help clean up the water. During the project, he also determined that bacteria can be used as a biomarker of the ecosystem's health.
"We had some cool technology that allowed us to use bacteria to tell whether or not there had been oil in the environment, even if we couldn't detect that oil with other methods typically used for environmental monitoring," he says.
These studies introduced Techtmann to DARPA. The agency was looking for ways to determine where ships had traveled without relying on tracking technology—some ships don't have it, and some find ways to fudge their logs. Techtmann proposed bacteria as an answer.
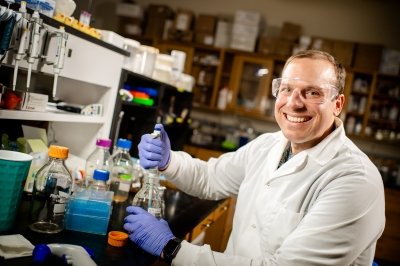
Techtmann’s award-winning work has made headlines around the world, capturing the public’s imagination with its novel approach and intent to benefit the greater good.
As he had learned in the Gulf, bacteria can work as an independent form of verification, like forensics. "The ship is like a fly trap for microbes as it's running through these ports," he says. "Someone working for the Coast Guard could take a swab off the side of the boat and put it in a device and know where the boat has been. If it doesn't agree with where the logs are saying, it might be worth looking into."
This project—Techtmann's initial collaboration with DARPA—won the agency's 2016 Young Faculty Award, which identifies and engages rising stars in junior research positions. The prize also forges links between researchers, DARPA, and the DoD—connections for potential future research.
Besides, Techtmann likes DARPA's mindset. "I really like how the agency is trying to develop new technology that the military can use but could also become more widely useful in society," he says.
He applied that filter when considering new projects. "I was looking for other opportunities to work with the DARPA mindset of, 'How can we move technology forward to address these really high-risk problems that have high reward?'" he explains. He went back to bacteria, and found a connection between oil-eating bacteria and plastic waste—essentially oil-based materials nobody wants.
Turning Plastic Into Food
The first step in Techtmann's process is to put the plastic through a reactor to break up the plastic's tough infrastructure and start breaking down those long polymer chains. This process turns the plastic into an oily substance, with carbon, oxygen, and hydrogen unlocked from the plastic's molecular structure.
That oily substance is then fed to hungry bacteria that thrive on those three elements and prefer them in that form. "We're taking bacteria that are really good with oily compounds and feeding them that pre-chewed-up plastic," says Techtmann. Bacteria grow quickly on this diet and make more bacteria cells, which are about 55 percent protein. Those cells are then dried out, and that's what becomes the protein powder.
Researchers also plan to use the process to create lubricant, giving another potential use for what was previously plastic trash.
At this stage in the research, the team knows that the plastic-to-protein-powder process works—on a lab bench. The next step is to have the entire system operate in one box that can recover 100 grams of protein powder by simply putting plastic into one end and retrieving protein powder on the other.
In the final phase of the project, the team will turn the box into a solar-powered, field-operational unit—one that can create kilograms of protein powder for as long as 28 days, but is small enough to fit into the back of a truck (or military vehicle).
"Plastic takes, at a minimum, a decade to break down in the environment. We could convert them into microbial cells in about a day," Techtmann says.
In the spirit of this research being developed for beyond just military use, the team is also working to be able to 3D print as many parts of the system as possible. They plan to make the design open source, so individual units can be quickly created and deployed by anyone who needs quick access to protein—especially nonprofits working in disaster relief.
"The goal is that, in the next two years or so, we have something that we can put out in the field somewhere and have it run for months at a time and still work effectively," Techtmann says. "We're starting to scale up now from small benchtop pieces to something that can process more plastic and make more protein powder."
Beyond Disaster Scenarios
Aside from feeding people in immediate need—whether that's soldiers or people displaced by natural disasters or warfare—Techtmann thinks protein powder made from plastic has much wider potential.
Plastic-sourced protein powder may sound odd now, but almonds and oats are used to produce dairy milk alternatives found in just about every grocery store and coffee shop—something unthinkable 40 years ago.
Plant-based food products in general are leaping forward into the public eye, with plant-based burgers simulating the taste and texture of meat making debuts at mainstream fast food chains like Burger King. Overall, the meat substitute market is expected to be worth $8.82 billion by 2027, according to Allied Market Research.
Techtmann sees a potentially similar path for plastic-based protein.
He realizes that the product would have an uphill marketing challenge. It's hard getting people to understand that they're eating bacteria, not plastic—never mind that the bacteria just happened to eat plastic for breakfast, lunch, and dinner. But he sees potential uses as part of the protein that makes protein bars, and with companies that make personalized food products and nutrition programs based on individuals' metabolic profile.
"Once we get the technology approved and the FDA gives the thumbs-up that we can eat this stuff, then we bring in the marketing to make it appealing and smell less like vegemite and more like sugar cookies," he says.
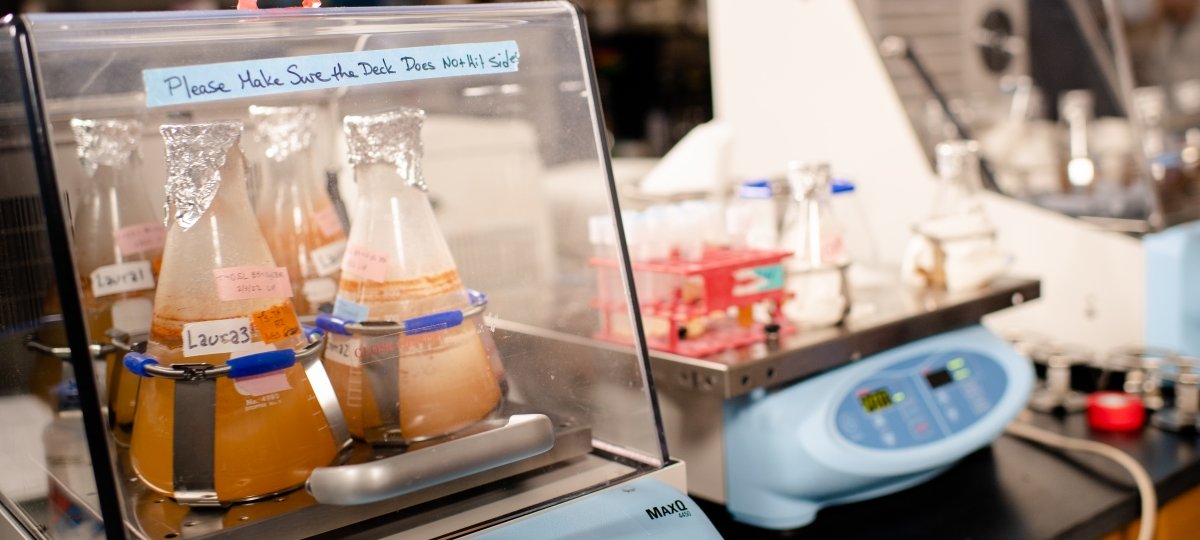
The BioPROTEIN project helps solve real-world problems and can also address national security capabilities.
The Scientist's Dream
Going from swabbing microbes off boats to creating a new food product might seem like a stretch, but Techtmann says it all lines up along the same two themes: finding new uses for bacteria and the greater good.
"At Michigan Tech, we're trying to solve big problems and put expertise at big problems," he says. "The walls between departments here are quite low." And, he added, faculty members help foster each other's creativity when it comes to science applications. "If we can take that curiosity and apply that to address big problems, then that's the scientist's dream."
Michigan Technological University is an R1 public research university founded in 1885 in Houghton, and is home to nearly 7,500 students from more than 60 countries around the world. Consistently ranked among the best universities in the country for return on investment, Michigan's flagship technological university offers more than 120 undergraduate and graduate degree programs in science and technology, engineering, computing, forestry, business, health professions, humanities, mathematics, social sciences, and the arts. The rural campus is situated just miles from Lake Superior in Michigan's Upper Peninsula, offering year-round opportunities for outdoor adventure.