228: Quantification and Mitigation of Boron from Recycled Steel in Cast Iron
The goal of this quantification and mitigation of boron project is to discover possible options to decrease boron in a cheap, effective manner when the current options are not sustainable for companies in the long term. This will decrease the metal waste from industry if boron can be expelled along with increasing material and mechanical properties of the metal sold to customers. Our team has been working with potential flux materials to trap the boron and discard it from the molten metal. We have been completing multiple experiments to analyze the material properties and elemental changes within our chosen flux material.
232: Shot Sleeve Re-design for Steel High Pressure Die Casting (HPDC)
High pressure die casting, HPDC, is a method traditionally used for the rapid casting of aluminum (Al) alloys into complex shapes, and recently there is garnered interest in using this process for steel alloys. HPDC is usually done with H13 steel as the shot sleeve and attempting to do the same HPDC process with stainless steel alloys, resulted in the failure of the H13 shot sleeve. To mitigate this predicted premature failure, an investigation of different ceramic materials to use as a liner inside the shot sleeve was performed.
234: The Effect of Alloying Composition and Casting Parameters on the Castability and Anodization of Aluminum
The goal of this project is to produce an aluminum alloy that can be gravity die-cast and anodized. This alloy will be used for the purpose of consumer electronics, such as in the cases of fitness bands and e-readers. For this reason, the alloy must be able to produce thin-walled castings with sufficient strength and elongation to survive wear and tear from daily use. Because Amazon’s incumbent alloy contains silicon for fluidity and strength, which cannot be anodized, the focus of this project is to limit the content of silicon in the alloy while maintaining sufficient fluidity and strength.
241: Wire Arc Additive Manufacturing and Heat Treatment of Al-Sc-Zr Alloys
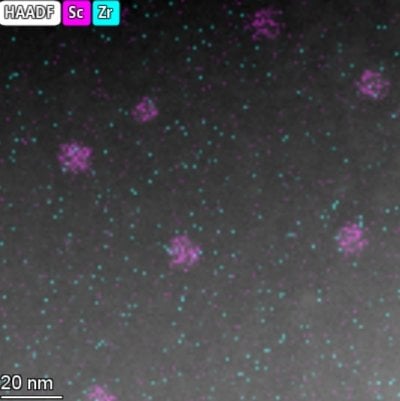
Wire arc additive manufacturing and heat treatment of Al-Sc-Zr alloys
Wire Arc Additive Manufacturing (WAAM) is an additive manufacturing process that allows for lower waste, energy requirements, and costs than traditional subtractive manufacturing. Aluminum WAAM is typically performed using standard aluminum welding filler wire alloys, which cannot be strengthened through heat treatment. The addition of Scandium and Zirconium allows the alloy to be heat-treatable while significantly improving the strength of the alloy. Our project seeks to understand the heat treat responses of a new aluminum alloy design by Hobart Brothers specifically for the creation of heat-treatable WAAM parts.