Simple. Scalable. Sustainable. Our 2020 Michigan Tech Research Award winner makes strides in recycling plastic waste.
No surprise, plastic melts when you heat it up. Done just right, melting down plastic could create a circular economy that ensures plastic gets recycled and reused instead of thrown out. The details of melting plastic to improve a wasteful big picture is the current focus of David Shonnard’s research.
Shonnard is a professor of chemical engineering, the Richard and Bonnie Robbins Chair in Sustainable Use of Materials and the director of the Sustainable Futures Institute at Michigan Technological University. He leads interdisciplinary teams studying biofuels and green chemistry using life cycle assessments for both products and industrial processes. Shonnard also heads the Tech Forward Sustainability and Resilience initiative.
Given the global scale of plastic waste — and the fact that takeout containers, clothes, pills and everything else we use plastics for are not going away overnight — it’s easy to feel guilt or dismay at the mere sight of a cafeteria spork. But Shonnard sees an opportunity instead.
Plastics come in many shapes and sizes, especially on the molecular level, which makes them difficult to recycle with ease. With heat and time, one kind of plastic can be turned into another. Within a reactor outfitted with a heated steel pipe that funnels plastic vapors, Shonnard and his team have been able to control melted plastic to make the end product tailored for reuse.
"Professor Shonnard has made a huge impact over the past 25 years in the field of sustainable engineering through research and education leadership. This award is a fitting tribute to recognize his contributions in the field of life cycle analysis, sustainability and biomass as a renewable feedstock for fuels and chemicals."
Q: What’s your research about?
DS: Technology enables a circular flow of recycling. Right now, waste plastics are a cost, but they could be of value if we can convert them back into other, reusable forms. If they have value, then they’re less likely to get thrown out.
This is a new research area for me, but it builds on decades of research we’ve done in biofuels. We’re taking the same processes we used to convert woody materials into biofuel and we’re now applying them to plastics. It’s a pivot rather than a completely new endeavor. The chemical industry is highly motivated to solve this plastics waste problem and they’re interested in the kind of chemical recycling technology we’re developing. I expect to see commercial versions within five years on a large scale and we are also working with our Office of Innovation and Commercialization to develop our own technology.
Q: How does the process work? What are the challenges you face?
DS: Picture if you accidentally left a yogurt container on a hot stove — don’t try this at home! — but if the stove was on high and you left the room, then when you came back, there likely wouldn’t be any container at all. That’s because plastic vaporizes in a hot, uncontrolled environment.
Our process takes place in a highly controlled environment. Waste plastic is introduced into a reactor to heat it up quickly without air, a process called pyrolysis, where we can control the temperature and how long the plastic stays in there. The reactor is quite simple: a single steel pipe with heat applied to the outside with two control knobs we can adjust — temperature and residence time. Many chemical processes in industry are simple like that. Lots of moving parts can break down, so the simpler the better. If you start with a large plastic molecule, heat and time will break it down. At a high temp for a long time, that big molecule will become many small, lightweight molecules; at a lower temp, we can produce higher-molecular-weight products. We tailor conditions of the reactor to make the material we want.
As chemical engineers, we’re accustomed to making these adjustments to processes. This is a simple, traditional approach applied to a new material.
"Dr. Shonnard is recognized nationally and internationally as a leader in sustainable engineering and advanced biofuels and bioproducts research … In addition, he has catalyzed a great deal of interdisciplinary research among researchers from many different departments at Michigan Tech, in collaboration with a host of international scholars."
Q: Where did you get the idea?
DS: I had been collaborating for years with a professor down in Mexico at the Universidad Autónoma de Yucatán in Mérida and we agreed to have one of his students come to Michigan Tech to study in my lab. The student, Ulises Gracida Alvarez, came with support from Mexico, and I needed to supply him with lab space and we decided to collaborate on a project. I had been reading about the plastics problems in the environment, so we discussed converting plastics through pyrolysis. He is now working as a postdoc at Argonne National Laboratory, continuing his research. He and I developed these concepts together; in fact, he’s a co-inventor on the invention disclosure. Now I have a new crop of graduate students carrying on this line of research into waste plastics conversion.
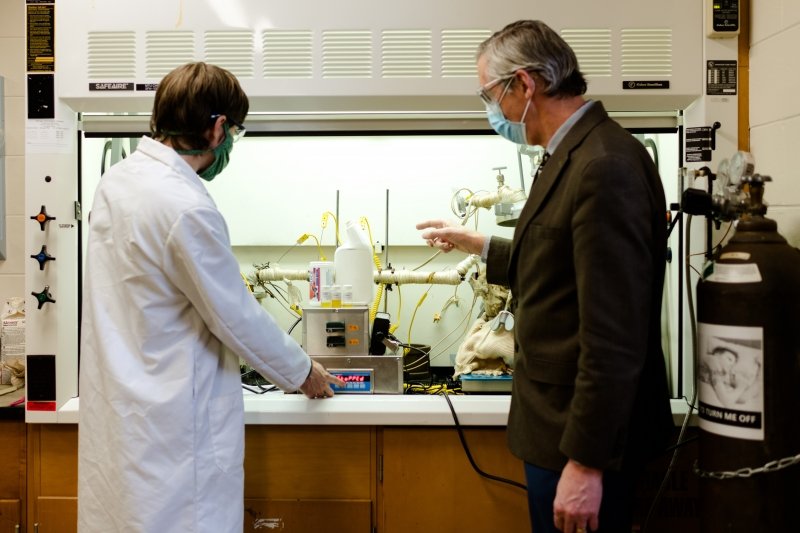
Q: The life cycle assessment (LCA) approach seems to be an important aspect. Can you explain more?
DS: We take a holistic approach with LCAs, which is a method to determine a technology’s environmental footprint from “cradle to grave.” In the waste plastics circular economy, the LCAs are conducted “cradle to cradle” because of the closed-loop recycling. We take a systemic view and look at the context to make the process perform better. This did influence how we thought about our pyrolysis project. It does make you think about a process as a part of a system and the downstream uses of your product. We sit in the middle of that value chain and we have to think about what our upstream supplier can provide in terms of waste plastic and what a downstream client needs — all while thinking about how the process fits in with low environmental impact. We need to come up with the simplest solution possible, to make it economical, lower emissions, more energy efficient. Which is a working definition of sustainability.
We investigate waste plastics conversion at multiple scales, too. We start at a small scale to figure out specific pyrolysis conditions and slowly scale up. With micropyrolyis we can study in great detail the chemistry that is happening. At larger scales, up to 1 kilogram per hour of waste plastic converted, we attempt to duplicate the results we observe at the small scale. Doing this takes the technology a step closer to real-world applications.
Q: Who benefits from your work?
DS: Over the years working on biofuel LCAs with companies, the benefits to the companies are that they learn of connections between their R&D and the environmental impacts in ways that they could not assess in-house. The knowledge that my group has can contribute directly to the mission of some of our partner companies. It isn’t just about making money in the current reality — companies care about the climate and about other impacts too. We think in more systematic and holistic ways than we used to. It has helped some of these companies improve their process technologies and interface effectively with regulatory agencies.
Q: What motivates you, then?
DS: As chemical engineers, traditionally we don’t get involved in the environmental realm as often as we should. We often investigate from a technical point of view. I’ve always asked, how can I weave in the health of the environment here? Considering how chemical engineering promotes sustainability motivates me. And working with students is very motivating — they come in, they’re novices in lab skills, they struggle with writing, then they grow. Their maturation process and their successes in their careers is satisfying to see. It’s all about the students. Yes, the technology is cool but without the students it has less meaning.
"Dr. Shonnard's research and education contributions to sustainable engineering have led to important advancements to the field and to society. Not only has his research been impactful, but his educational and graduate student mentoring has impacted hundreds of graduates and their knowledge of sustainability across his career."
Michigan Technological University is an R1 public research university founded in 1885 in Houghton, and is home to nearly 7,500 students from more than 60 countries around the world. Consistently ranked among the best universities in the country for return on investment, Michigan's flagship technological university offers more than 120 undergraduate and graduate degree programs in science and technology, engineering, computing, forestry, business, health professions, humanities, mathematics, social sciences, and the arts. The rural campus is situated just miles from Lake Superior in Michigan's Upper Peninsula, offering year-round opportunities for outdoor adventure.
Comments