Michigan Technological University’s Van Pelt and Opie Library may be more solitary than ever these days, but it isn't quiet. The library's 3D printers are running full blast, turning out thousands of face shields for community health workers.
Huskies seeking silence would instead find a mini manufacturing center operated by library staff David Holden and John Schneiderhan alongside engineer Joshua Pearce. Together with others across campus and the community, they are tapping the University’s brainpower and equipment to stem the spread of COVID-19. For now, it’s face shields, but plans are in the works to produce other items in short supply, including the swabs essential to COVID-19 testing and National Institutes of Health (NIH) face masks.
The Western Upper Peninsula Health Department (WUPHD) has been an active partner every step of the way. "We are very fortunate
to have Michigan Tech engaged in the COVID-19 response locally,” said Pete Baril,
WUPHD director of planning and community preparedness. “This face shield project is
a great example of the partnership between MTU and the community."
"The Western UP Health Department alone has distributed well over a thousand of these shields to partners ranging from law enforcement, to hospitals, to funeral homes."
Providing PPE and other 3D-printed devices is a logical fit with the teaching, research
and community service at the core of the University’s mission. Whether on or off campus,
everyone has been stepping up. Faculty and students transitioned to remote learning. Faculty researchers designed and built a Mobile Thermal Unit Sanitizer and opened a COVID-19 testing lab. New innovations continue to roll out as Huskies
look to the future.
3D PPE at MTU
In this Q&A, Holden, the library’s manager of technology and innovation; Schneiderhan, library technologist; and Pearce, a professor in materials and electrical engineering known for his work in open-source initiatives, including ventilator designs, talk about when and how the 3D PPE project got started, where it’s headed and why it’s important.
Q: How long have you been printing and how long do you think it will continue?
DH: Our first recorded production was on March 25 and our first delivered product was on March 26. We initially started with a couple of different designs that were circulating within the open-source community. We finally reached agreement on a customization of one of those designs on April 1, using guidance and feedback received from health care workers and the local health department. How long all this will continue is unknown. Eventually, supply chains will stabilize and supply face shields, respirators and masks as needed where needed, but that is taking more time than any of us anticipated. The other area of work, swabs for COVID-19 testing, is potentially a longer-term engagement to ensure local demand for ongoing testing is covered.
JS: We are thankful for the University and management to support us in this endeavor and will continue to work to support the local health care community however we can for as long as we are able.
Q: You’ve printed more than 2,500 face shields so far. Where have they been donated in our community?
DH: The majority have gone to the Western UP Health Department for distribution. We worked with the WUPHD to facilitate modification reviews and design approval with the hospitals before going into production. We have also distributed them to local law enforcement organizations, hospital in-house laboratories, the state of Michigan Department of Health and Human Services, Copper Country Mental Health Services, several dental offices and even our own facilities team.
"John and David have been great to work with — they tweaked the design several times based on feedback we gave them. This quick response in design and production has been very well received by the many groups we have distributed the shields to."
Q: Tell us about your role in the project and why you’re involved.
DH: Joshua and John are the technical engine of the team, researching designs and materials, tuning the equipment, prepping the print files and looking into opportunities for greater involvement. My role draws on my industrial management background as more of a production coordinator. I serve as a point of contact for people looking for PPE, helping with production process design, product distribution, assembly, packaging, finding materials, quality inspection and keeping the equipment in the library producing.
JS: My role with face shields, swabs, ventilation splitters and face mask respirators has been initial prototyping and troubleshooting their production on the specific equipment we are using for each of these products. I am also keeping the equipment running when trouble arises with the printers, assembling finished products and working with David and Joshua on process design for each of the different products.
JP: My research students have been working with David and John in the library to print PPE for local hospitals. Bharath Lavu, a graduate materials science and engineering student, has been particularly productive and helpful. We are also formally researching several other areas of COVID-19 technologies, including ventilators, nasal swabs and high-temperature 3D printers for making thermally sterilizable and reusable PPE.
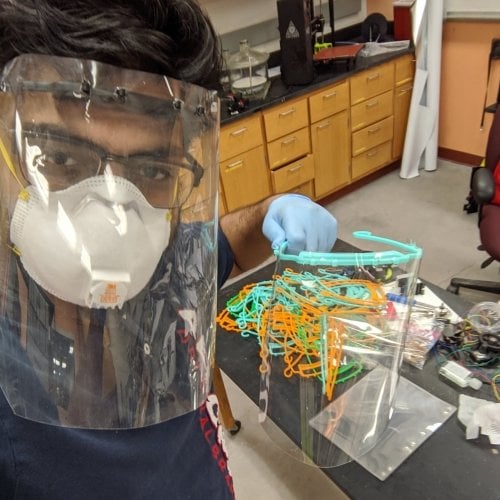
Q: The shields cost a little over a dollar in materials to produce. What are the materials
and where are you getting them?
DH: The shield consists of three parts: a halo that fits flexibly around the head and against the forehead; a clear polyester sheet, 9.5 by 11.5 inches, that is punched and snaps onto the halo; and an elastic band that fits across the back that tensions the halo for proper fit.
The halo is 3D printed using whatever filament/resin we can get our hands on in quantity: PLA, NGEN, PETG. John continually searches for it and we have gotten donations of materials from faculty members. The polyester sheet (think Mylar) has been the toughest item to come by. We have scrounged an old roll of 5 mil (0.05 inches) from library storage, experimented with roll laminate donated from the Keweenaw National Historical Park (what great people!), spare sheets at cost from The Print Shop downtown, and our library coordinator, Mia, has been shaking the trees for plastic suppliers with material in stock from New York to San Diego. It really has been a group effort. The elastic bands have been No. 32 rubber bands from Walmart — 27 bags of them so far.
"I'm sure some inventory manager in Arkansas is scratching their head saying, 'Toilet paper? Sure ... But what's with all the rubber bands?'"
The last bit, of course, is the 3D printers to make it happen. We have three excellent printers in the library that are awesome (thank you, C2E2 folks!), but we also have two on loan from the Makerspace thanks to Mary Raber from the Pavlis Honors College, and two from the math department thanks to Cécile Piret. That is just the library.
JS: Dale Dewald has also offered up the use of the MSE/Ultimaker 3D printer, which has been useful for printing valve Y-splitters for the ventilators.
JP: In the M&M [Mineral and Materials Engineering Building], we have a large fleet of different types of open-source 3D printers, many of which the students built themselves. Hundreds of MTU students have taken the Open Source 3D Printing course where they take home their own self-built 3D printer.
"I have heard from several students who are printing PPE for their local communities with the printers they made in class, both downstate as well as in other countries. Honestly, I am really proud of them."
Many of our lab’s printers are used for printing PPE whenever they are not actively being used by the students on their research projects. We have burned through dozens of spools of filament and used all of our leftovers.
How You Can Help
Superior Ideas, Michigan Tech’s crowdfunding website, supports efforts to bolster COVID-19 prevention and testing. In addition to the 3D PPE manufacturing happening on campus, another project, led by Ebenezer Tumban, molecular virologist and vaccinologist, has so far supplied approximately 2,000 samples of viral transport medium to UP health care facilities.
The medium, which is in short supply, is essential to preserve COVID-19 test specimens. Michigan Tech has provided samples to four Upper Peninsula health care facilities, including UP Health System-Portage, Baraga County Memorial Hospital, Houghton County Medical Care Facility (Canal View), and OSF-St. Francis Hospital.
Q: What about the more sophisticated and durable filtered face mask you’re working on? What kind of materials are needed, and what stage of development is it in?
JP: Noah Skrzypczak, a student in my research group, designed and built a high-temperature 3D printer that is capable of printing polycarbonate, Ultem and PEEK — all high-temperature, high-strength engineering plastics. The idea of making masks out of these materials is that you could heat-sterilize the mask (normal materials like PLA or PETG would melt) and only need to replace the actual filter material after cooking it. We are just testing this now, but it looks promising. These masks would be more expensive because these materials are more costly and will need funding to pursue this, but they would be much easier to sterilize in something like the MTU Mobile Thermal Sanitizer.
DH: In the library, we are working through the manufacturing details of an NIH-approved design. It consists of 25 individually printed parts, six sheets of filter material, and various gaskets and straps. We have produced five prototypes so far and are beginning the trafficking process to get local approval on the design.
Q: What’s the anatomy of a face mask and how is it assembled? Is it difficult to put together?
DH: This is an approximate exploded-parts diagram of the NIH-approved design. It is a complex assembly at this point: 25 printed pieces, six filters, and various straps/gaskets to ensure proper fit, and so is not ideal. We are in the process of customizing the design to make the replacement of the filters simple, and are designing filter replacement kits and instructions to make cleaning and replacement a straightforward matter. As Dr. Pearce has noted, any customizations/templates are shared back into the open-source community.
Q: There’s also a test swab project. How is that developing?
JP: The US as a whole and the UP specifically do not have nearly enough COVID-19 tests. This is one of the major reasons why most other countries are doing much better than we are at controlling the spread of the disease. One challenge is the short supply of swabs — just fancy Q-tips. We have started printing them in our lab with the Open Source Hardware Enterprise’s open-source SLA printer, and John has been using the undergraduate biomed printers. We are having the swabs tested now by local doctors. If they are OK, we will start manufacturing them for the MTU COVID-19 diagnostic lab. Several universities and the US military have been printing swabs — what we hope to add is a way to print the "business end" on the slower, smaller SLA printers, and then handles on our much more numerous and fast extrusion printers. With this trick, we hope to be able to cover local demand by being able to make more swabs with our equipment. We will, of course, share everything open source so everyone else can use it in their own communities.
JS: We would like to thank Dr. Sean Kirkpatrick for the use of the M&M U106 lab/SLA Formlabs2 printers. This is helping us produce batches of samples to test the structure, durability, and functionality of the different designs with a variety of materials.

Q: What's something you've learned through this project?
DH: The weeks have been a blur — I have a scattered, fragmentary set of impressions:
• We have been at this for many weeks and I would have expected that an enterprising
manufacturer would have stepped into the picture and satisfied the regional demand.
Instead, there are active public maker groups here in Houghton and an even larger one in the Marquette area that are manufacturing a variety of
items, including PPE, and exporting them as far as downstate. This underscores to
me the versatility of 3D technology and the tremendous spirit of collaboration and
creation in the open-source community.
• The number of people on campus in a diverse set of roles who offer help and are
so capable and insightful is humbling. My eyes are opened up to the power of this
University to make good things happen.
• Working with Dr. Pearce and understanding the concerns a world-class researcher
has in developing a product — and the concerns he knows to put aside at the right
time — is knowledge I have picked up and will use in my own projects when this is
all behind us.
• Understanding that even with a standards-compliant/national-organization-approved
design or product, you have to listen to the end user and craft the solution that
works best for them in their specific environment.
Q: Michigan Tech joins a legion of educational institutions around the country that are 3D-printing PPE. Anything you’d like to say to your fellow volunteers? Are there any projects out there that you find particularly inspiring?
DH: Working with the local health department has been a critical factor in successfully navigating the confederation of health care institutions in the community. Otherwise, just encouragement to share designs, instructions and templates within the framework of the open-source community so we can all riff off of each other’s ideas and successes.
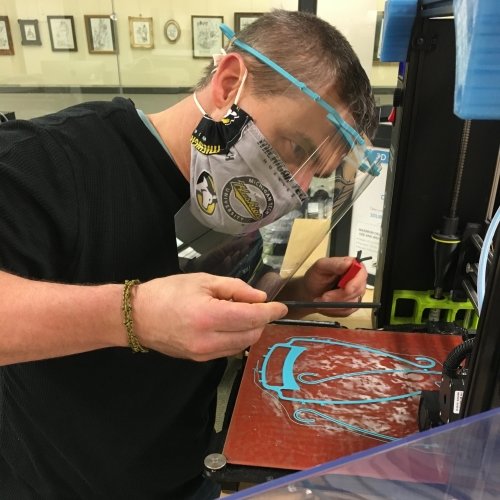
Looking Forward
And the printers print on — seven of them on the second floor, running continually throughout the day. "They can be noisy. To break it up, we are playing a lot of really loud music,” said Holden. “Grateful Dead, Jimi, Oingo Boingo. We both like '70s rock, so a good bit of Zeppelin, Clapton, Traffic. Also a fair amount of blues — Robert Cray and R.L. Burnside stick out. As loud as we can play it.”
Schneiderhan said the building's emptiness is harder to contend with than the noise. “I for sure miss the interaction and collaboration with the faculty and staff, but what I miss most of all are the students and their energy,” he said.
There are bright spots, though. "I see students posing outside in front of the Husky statue, or working on the PPE project in the MSE/MOST lab — socially distanced today with aspirations of a brighter tomorrow," said Schneiderhan. "There is hope!"
Michigan Technological University is an R1 public research university founded in 1885 in Houghton, and is home to nearly 7,500 students from more than 60 countries around the world. Consistently ranked among the best universities in the country for return on investment, Michigan's flagship technological university offers more than 120 undergraduate and graduate degree programs in science and technology, engineering, computing, forestry, business, health professions, humanities, mathematics, social sciences, and the arts. The rural campus is situated just miles from Lake Superior in Michigan's Upper Peninsula, offering year-round opportunities for outdoor adventure.
Comments